Environmental Stewardship
The nature of what we do
Environmental stewardship is deeply rooted in our company and is a strong foundation of our sustainability work. Every action we take and decision we make considers the long-term view — for our company and for the ecosystems in our care. To ensure our forests remain healthy and productive for generations to come, we are dedicated to protecting and enhancing the many additional benefits they provide, such as clean water, clean air and wildlife habitat, while also leveraging ecosystem services to provide climate solutions — such as through mitigation banking and renewable energy development — that benefit society and our world as a whole.
We are also committed to minimizing the environmental footprint of our wood products manufacturing business, including reducing air emissions, limiting waste and maximizing wood recovery. These actions are smart for our business, good for the environment and essential to running our operations sustainably. We are proud of our excellent performance in environmental stewardship. We are also firmly committed to finding innovative, meaningful ways to continually improve our practices through ongoing scientific research and cross-functional partnerships.
Practicing Sustainable Forestry
As a pioneer in sustainable forestry, we manage our forests to ensure a sustainable supply of wood for our customers while protecting the other important benefits forests provide.
Protecting Biodiversity
Our forests provide much more than timber. They are thriving, healthy ecosystems that we are honored to steward.
Improving Conservation Outcomes
We participate in multiple programs to ensure our forests provide habitat features that support at-risk, sensitive, or threatened and endangered species.
Contributing to Clean Water
Our forests are critical sources of clean water for communities in our watersheds, and we are committed to protecting aquatic ecosystems on our lands and around our manufacturing sites.
Storing Carbon
Sustainable forests and wood products play an important role in mitigating the effects of climate change by absorbing carbon dioxide and storing carbon.
Making Better Energy Choices
We meet more than 70 percent of our energy needs from renewable biomass and are actively working to improve our energy efficiency. We also have a growing solar and wind power lease program.
Decreasing Our Emissions
We continually seek new ways to decrease our contribution to greenhouse gas emissions and reduce air emissions from other sources.
Verifying with Certification
We prove our strong performance in sustainable forest management and wood fiber procurement through externally validated certification programs.
Minimizing Waste
We find creative, responsible and beneficial uses for our wood residuals and work to reduce waste generated in our manufacturing process.
Responsible Wood Procurement
We ensure that all the wood entering our facilities is from responsibly managed forests.
PRACTICING SUSTAINABLE FORESTRY
As one of the world's oldest and largest private timberland owners, we've been growing, harvesting and regrowing forests for more than a century. We have been proving forests can be managed sustainably for a very long time — ensuring our customers have access to a renewable supply of wood while protecting the other important benefits forests provide.
- 1922: Weyerhaeuser donates 5,000 acres of forest for Washington state reforestation experiments.
- 1925: We advocate for legislation to encourage reforestation after harvest — an uncommon practice at the time.
- 1937: We begin research into sustainable-yield forestry, which ensures harvesting does not diminish the forest's ability to provide the timber volume in the future.
- 1938: We are one of the first companies to successfully grow and plant tree seedlings. From this effort, a new crop was born, and Weyerhaeuser's tree-planting era began.
- 1941: We establish the first certified tree farm in the United States, located on 120,000 acres of harvested and fire-burned land in Washington state.
- 1986: We plant our 2 billionth seedling in the blast zone of Mount St. Helens, marking the completion of a massive restoration effort in which we planted 18 million seedlings by hand following the 1980 eruption.
- 1994: We hold town hall meetings in Washington and Oregon attended by more than 2,000 people, who raised ideas, asked pointed questions and leveled criticism at the company. These public meetings were instrumental to the integration of more extensive environmental applications into our management practices.
- 2006: We are one of the first companies to register our timberlands to be certified to the Sustainable Forestry Initiative® Forest Management Standard, a third-party sustainable forestry certification.
- 2013: We achieve 100 percent certification of our timberlands to third-party sustainable forestry standards.
- 2020: We launch our 3 by 30 Sustainability Ambitions, which intensify our commitment to make meaningful progress to help solve three big challenges facing the world — the need to provide climate change solutions, provide more sustainable homes, and support thriving rural communities — by 2030.
Today, we continue to certify 100 percent of our forests to the SFI® Forest Management Standard. We plant about 130 to 150 million seedlings per year in our harvested sites, equivalent to almost four trees per second, and we are transparent about our harvesting and planting metrics.
Everyday
Sustainability
Sustainable Forestry
A Remarkable Renewable Resource
We always grow more trees than we harvest to ensure we have a renewable cycle of forests that last forever.
Video
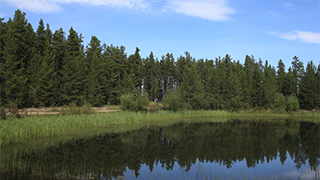
Management Agreement Renewed in Alberta
After an extensive, collaborative process including forest and wildlife inventories and engagement with local communities and First Nations, we successfully renewed our Forest Management Agreement with the province of Alberta.
Blog Post
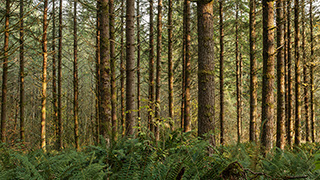
Timberlands: Sustainable Forestry
Sustainable forest management practices are at the core of our timberlands business strategy.
Business Integration
Back to Environmental Stewardship Overview
Our forests are much more than timber: They are thriving, resilient ecosystems that we help steward. All the living things in a forest — from the mightiest trees to the tiniest microbes — interact with each other and with the soil, water and air to form complex ecosystems that support a wide range of plant and animal communities.
The forests we manage host hundreds of native vertebrate species, including large mammals such as deer, elk, cougar, black bear and bobcat, as well as a tremendous diversity of birds, reptiles, amphibians, insects, native fish and other aquatic species. Each of these species needs something different from their habitat, including different forest age classes and structures, and other important features such as healthy riparian areas. Since our millions of acres of timberlands contain a range of forest stand ages and structures, along with protected areas around streams and wetlands, these forests support a high level of native biodiversity.
To preserve and protect the ecosystem balance, we regularly conduct biodiversity assessments across our forests. These assessments, which include analyzing species occurrence data and monitoring for the presence of threatened or endangered species, guide and inform our implementation of habitat conservation and species management plans. These include leaving buffers along riparian areas, surveying sites for species occurrences prior to harvesting and thinning activities, refraining from harvest during certain times and managing for specific habitats using prescribed burns or thinning harvests.
Because we sustainably manage our forests, we can simultaneously deliver renewable fiber to the market and a myriad of other ecosystem services — such as clean water and recreation opportunities — to surrounding environments and communities.
Everyday
Sustainability
Biodiversity
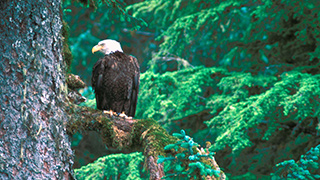
How We Do It: Wildlife Habitat
Learn more about our approach to managing wildlife habitat in our working forests.
Printable Resource
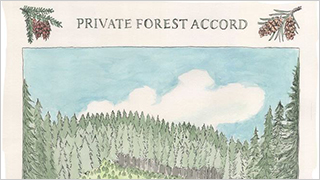
Private Forest Accord
We helped negotiate a landmark agreement to update forest practices in Oregon, including efforts to protect the state’s iconic salmon population and other sensitive species.
Blog Post
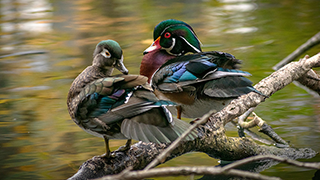
No Harm, Lots of Fowl
In March, 2022, we formally signed a five-year Memorandum of Understanding with Ducks Unlimited Canada to help conserve sensitive wetland habitats.
Blog Post
Back to Environmental Stewardship Overview
Improving Conservation Outcomes
Ensuring our forests provide habitat features that help us manage for at-risk, sensitive or threatened and endangered species is a core component of our environmental stewardship. We create and preserve critical habitat through multiple programs, including conservation easements and agreements, mitigation banking, and formal Habitat Conservation Plans and similar arrangements with the U.S. federal government.
Combined with our sustainable forest management practices, conservation easements and other local agreements can enhance the long-term stewardship and protection of wildlife habitat, biodiversity and recreational access. These partnerships are made with a variety of groups and organizations, and they allow us to continue managing our forest resources, which helps protect the economic benefits of our working forests. Habitat Conservation Plans are administered under the U.S. Endangered Species Act and provide specific guidance on the protection and enhancement of habitats for threatened and endangered species. We currently participate in HCPs and other conservation agreements in Alabama, Arkansas, Florida, Georgia, Louisiana, Maine, Mississippi, New Hampshire, North Carolina, Oklahoma, Oregon, South Carolina, Vermont and Washington.
Authorized through the U.S. Clean Water Act, mitigation banking allows us to set aside certain areas of our timberlands to preserve, enhance or restore a wetland, stream or other habitat area to compensate for development by another entity in a similar nearby ecosystem. Mitigation banks are regulated and approved by the U.S. Army Corps of Engineers and a consortium of federal, state and local agencies. We currently operate 14 mitigation banks and projects, primarily in the U.S. South. Several other projects are in various stages of evaluation and development.
We have more than 3.6 million acres invested in these conservation programs across our Northern, Southern and Western Timberlands, and we are always looking for new opportunities and partnerships to have a beneficial impact on biodiversity and conservation.
Everyday
Sustainability
Improving Conservation Outcomes
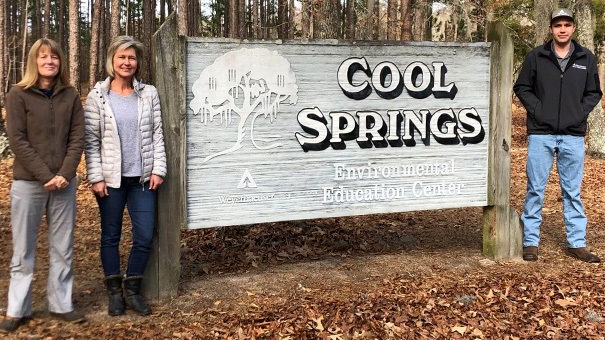
6,700 Acres and Counting
As part of our long-term partnership with the Coastal Land Trust in North Carolina, we worked on an agreement to transfer sensitive wildlife habitat along the Cape Fear River into their care.
Blog Post
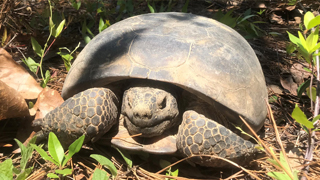
The Tortoise Wins in This Race
The gopher tortoise is getting a boost on our land in Mississippi, where we are maintaining 1,260 acres of upland pine habitat to support this threatened species, which digs gopherlike burrows for shelter.
Blog Post
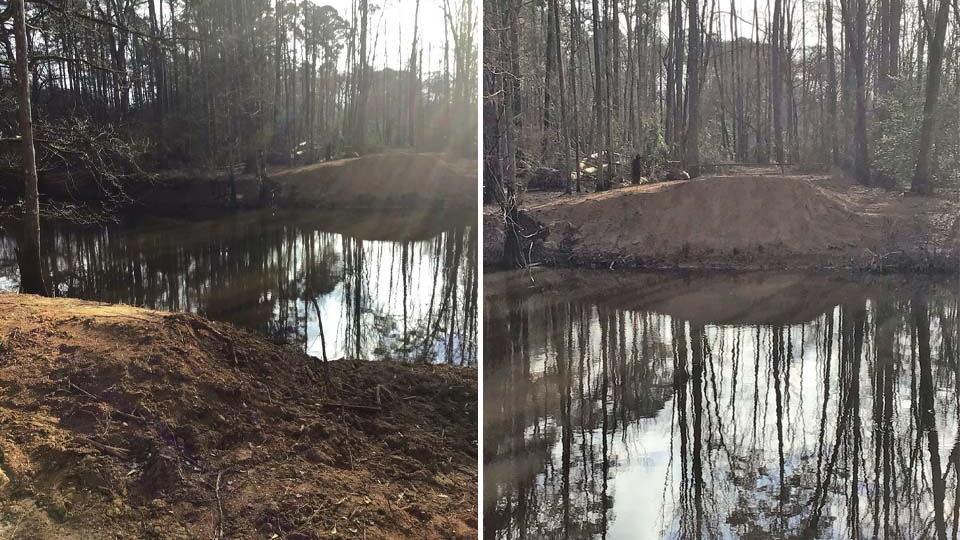
Transforming Acreage for Critical Fish Habitat
A complete reconfiguration of dikes along the Coos River in Oregon opened up 11 acres of land for critical fish habitat while safeguarding nearby homes from flooding.
Blog Post
Back to Environmental Stewardship Overview
Our forests are critical for providing clean water to communities in our watersheds. The trees, plants and soil absorb rain and snowmelt, filter and then slowly release clean water into the many streams, rivers and groundwater systems on our lands. From harvesting to road building, our sustainable forestry practices safeguard water quality by maintaining our forests' ability to capture and filter water — for people, fish and countless other organisms.
Because our forests rely on natural precipitation (rainwater and snow) to grow, our company’s measurable impact on water use is limited to our wood products manufacturing sites and offices, where water is either recycled or treated on-site, evaporated while products are drying or delivered to a local, publicly owned treatment facility. Even with this minor amount of water use at our mills, we continue to stay focused on reducing water use wherever possible.
Everyday
Sustainability
Clean Water
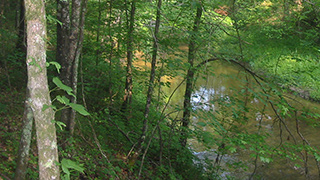
Mitigation Banking
We offer wetland and stream mitigation solutions to keep the environment in balance.
Business Integration
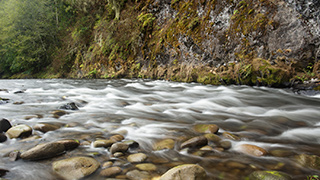
How We Do It: Riparian Buffers
We leave tree buffers along waterways to reduce siltation and protect aquatic habitat.
Printable Resource
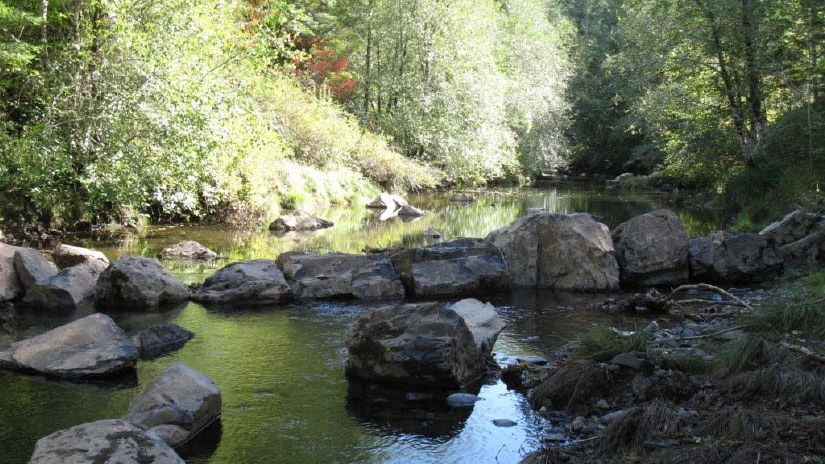
An Honor by the Coast Fork Willamette Watershed Council
We’re proud to work with the Coast Fork Willamette Watershed Council to improve water quality and fish habitat through restoration, monitoring, education and stewardship.
Blog Post
Back to Environmental Stewardship Overview
Sustainably managed forests are a critical part of climate change mitigation. As our millions of acres of forests grow, they absorb carbon dioxide from the atmosphere and store it as carbon in their trunks, limbs and roots, as well as in the soil. After our trees are harvested and made into long-lived wood products, much of their carbon remains stored for the life of those products. After harvest, we plant millions more trees, which immediately begin absorbing more CO2 from the atmosphere, and the next round of wood products store more carbon yet again — all part of an amazing sustainable cycle.
Our managed forests mature quickly and are often able to sequester more carbon than unmanaged forests through faster, continuous rotations, all while maintaining the vast pool of carbon in the forest soil.
When we turn logs into wood products and those wood products are used to create buildings, that carbon is locked into the product for the life of the building. And in addition to storing carbon, using wood for construction requires less energy than other non-renewable building materials, such as steel and concrete, resulting in fewer greenhouse gas emissions. Our Carbon Record provides a detailed accounting of the carbon that is sequestered by the forests we manage and stored in the wood products we make.
Everyday
Sustainability
Carbon storage
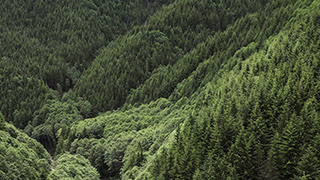
How We Do It: Forest Carbon
Our forests store between 2.3 billion and 3.6 billion metric tons of CO2. That is the same number of emissions generated by providing every home in the United States with electricity for three to five years.
Printable Resource
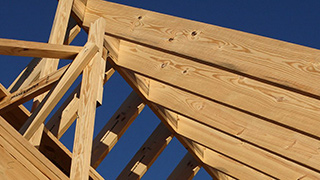
Building Sustainably with Wood
Wood products made from wood sourced from well-managed forests is the ultimate renewable, sustainable choice of building material.
Business Integration
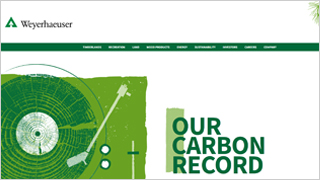
Our Carbon Record
Explore the story of our carbon emissions, removals and storage, as well as our ambitious target to further reduce greenhouse gas emissions across our operations.
Positive Impact Area
Back to Environmental Stewardship Overview
We meet more than 70 percent of our manufacturing facilities’ energy needs from renewable biomass, using what would otherwise be wood waste either from our forest or manufacturing operations to create our own energy. This approach allows us to reduce our reliance on nonrenewable fossil fuels and purchased electricity.
In 2022, we continued our efforts to becomes a leader in energy independence and sustainable, cost-efficient operations. Each of our manufacturing sites now has a designated energy champion who is responsible for short-term action plans to improve energy efficiency. We also integrated greenhouse gas considerations into our capital planning processes to strategically allocate capital toward reducing our carbon footprint.
These actions support our commitment to the U.S. Department of Energy’s Better Plants Program to improve energy efficiency at our manufacturing facilities by 10 percent between 2020 and 2030, and to reduce our Scope 1 and 2 greenhouse gas emissions by 42 percent within the same time period. We are well on our way to meeting these goals.
We also play a role in other renewable energy solutions. Our timberlands provide an important land base for renewable energy production, such as wind and solar power. And we supply other mills, companies and utilities with woody biomass used to produce renewable, carbon-neutral energy.
Everyday
Sustainability
Energy Choices
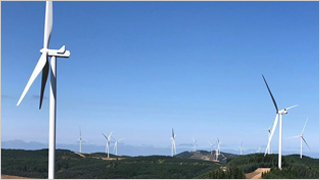
Supporting Wind Energy Development
The Skookumchuck Wind Facility, opened in 2020 and operated by Southern Power, is part of a growing portfolio of renewable energy projects within our Natural Climate Solutions business.
Blog Post
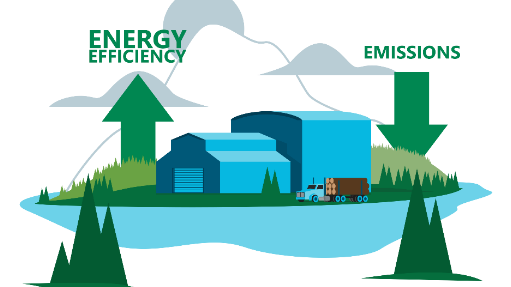
Energy Efficiency in Our Wood Products Business
Learn about our proactive, in-depth approach to managing our energy usage within our manufacturing and distribution facilities.
Printable Resource
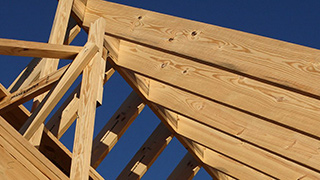
Building Sustainably with Wood
Independent life-cycle assessments substantiate the low energy intensity of wood products.
Business Integration
Back to Environmental Stewardship Overview
To keep global temperatures from rising to catastrophic levels, the business community must continue to reduce greenhouse gas emissions. As a company, we continually seek to decrease our contribution to greenhouse gas emissions and other pollutants such as carbon monoxide and volatile organic compounds.
Between 2000 and 2020, we reduced our total greenhouse gas emissions by 57 percent — but we aren’t going to stop there. In 2021, we set new GHG emission reduction targets that align with the need to limit global warming to 1.5 degrees Celsius. These ambitious targets include reducing our Scope 1 and 2 emissions by 42 percent and our Scope 3 emissions by 25 percent per unit of production by 2030.
To achieve these goals, we are laser-focused on realizing energy efficiency in our mills, increasing our use of renewable energy, and working to decrease emissions associated with our timberlands operations. Additionally, we have made significant improvements in reducing other emissions, including capital investments at several mills to implement cleaner-burning units, energy optimization and upgrades to emission control systems.
Everyday
Sustainability
Decreasing Emissions
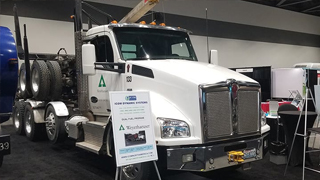
Propane Power
Since 2016, we have been converting trucks to run on propane to reduce emissions in our Western Timberlands operations.
Blog Post
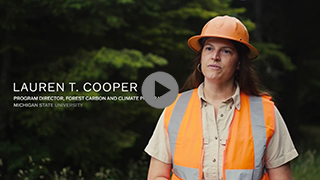
Contributing to Climate Change Solutions
Sustainably managed working forests and wood products are important tools to reduce the concentration of carbon dioxide in our atmosphere. Learn why in this video that explores our 3 by 30 Sustainability Ambition focused on climate solutions.
Video
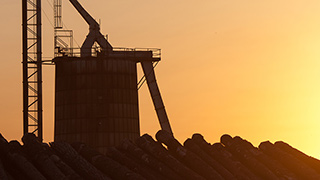
Air Emissions by the Numbers
We share our air emissions data by emission category and our total greenhouse gas emissions annually in our sustainability data.
Data
Back to Environmental Stewardship Overview
We strive to use as much of each log as possible and continually seek new outlets for our manufacturing byproducts and used equipment.
On average, 95 percent of each log that enters our mills is turned into a useful product. The primary products we produce are solid lumber, wood panels and engineered wood products — our core product lines. Wood shavings, sawdust, chips and bark are sold or delivered to downstream customers who make other useful and essential products. Toilet paper, diapers, paper, cartons, boxes, bags, landscaping mulch and wood pellets are just a few of the countless products made from our wood fiber and forest and mill byproducts.
Still, we are always looking for ways to reduce the amount of overall waste we generate, including finding responsible methods for reuse and recycling. On average, we reuse, recycle or repurpose 99 percent of what could have been waste in our operations — the equivalent of more than 12 billion pounds of material each year that otherwise would have found its way to a landfill.
Everyday
Sustainability
Minimizing Waste
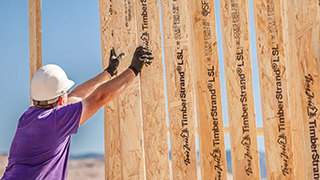
TimberStrand® LSL
The manufacturing process for TimberStrand® LSL produces high-performing engineered lumber using small-diameter trees that are not strong or straight enough on their own to be of structural value.
Business Integration
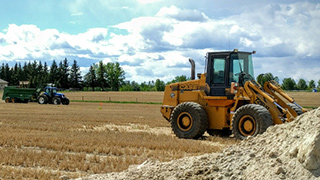
From Aspens to Ashes
Our team in Edson, Alberta, takes the ashes from burning renewable biomass and sends them to regional farmers rather than landfills.
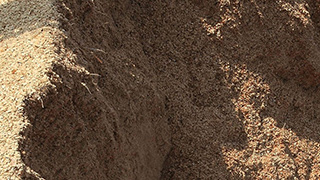
Waste Reduction by the Numbers
We are transparent about how much waste we produce — and divert to other uses — in our annual sustainability data.
Data
Back to Environmental Stewardship Overview
To prove our forest management and wood fiber procurement practices are sustainable, we participate in independent certification programs for forest management, fiber sourcing and chain of custody. Our entire portfolio of timberlands is certified to the Sustainable Forestry Initiative® Forest Management Standard — compared with only 11 percent of the world's forests that are certified today.
Internationally recognized forest certification standards — such as SFI®, Programme for the Endorsement of Forest Certification, the American Tree Farm System and the Forest Stewardship Council — provide customers and stakeholders with an objective, third-party determination of whether companies are implementing sustainable forestry practices and making products that come from legal and well-managed sources. We are vocal supporters of the importance of these standards and the use of independent, third-party audits to verify compliance and promote sustainable forestry around the world.
At Weyerhaeuser, we choose to certify our timberlands and operations to SFI’s standards because they are strong, science-based standards that have effectively pushed forestry in a more sustainable direction. The SFI standards are designed specifically for operations in North America, and we value SFI’s collaborative approach, especially around logger training and the requirement to invest in research and apply it to our operations. Recent updates to the SFI standard include an increased focus on protecting biodiversity, engaging with Indigenous peoples, promoting fire resiliency and mitigating and adapting to climate change.
In addition to our forests, we certify all of our manufacturing facilities to the SFI Fiber Sourcing or Certified Sourcing standards, and select sites are certified to the SFI and PEFC Chain of Custody standards.
Our Certificates
Forest Management
Fiber Sourcing
Chain of Custody
Certified Sourcing
Back to Environmental Stewardship Overview
On average, we source 40 percent of the wood used to make our products from our own SFI-certified forests, about 15 percent from other certified landowners, and the remaining 44 percent from noncertified landowners — typically small, family-owned forests. Whether wood comes from a certified forest or not, we ensure all the fiber we use to make our products is from legal, noncontroversial and responsible sources.
Our approach to responsible sourcing is guided by our Wood Procurement Policy and our certification to the SFI Fiber Sourcing Standard. This process includes positively influencing the forest practices of the landowners we buy logs from through actions such as requiring best management practices for protecting water quality and wildlife, requiring the use of trained loggers and sharing sustainable forestry information with landowners.
Everyday
Sustainability
Responsible Procurement
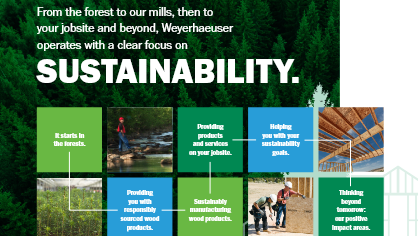
Building Sustainably with Wood
The benefits of building with wood start with forest management and carry all the way to a the product’s use in a home.
Business Integration
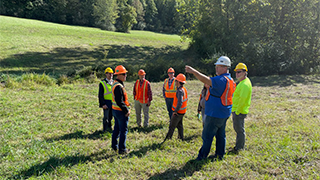
Our Ongoing Commitment Leads to Successful Audits
For decades, our committed staff have rigorously maintained full compliance with third-party sustainability standards through ongoing training and oversight.
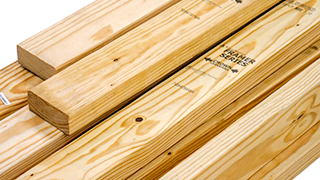
Responsible Sourcing by the Numbers
We transparently share and update data annually about our fiber sourcing.
Data
By using this website, you agree to our Privacy Policy. California residents: See our CCPA Privacy Notice for details on what personal information we collect and for what purposes.