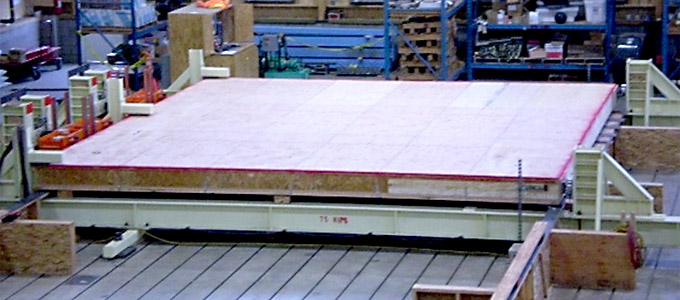
Demands on prefabricated wood I-joists in engineered buildings extend to more than just gravity requirements. Seismic and wind lateral forces induce diaphragm shear interactions that the engineer of record needs to evaluate when specifying I-joists in light-framed diaphragm applications. In this post, I’ll provide some background on I-joist diaphragms and detailed information on the use of our TJI joists in engineered diaphragms.
Today’s engineered wood products allow engineers to span diaphragms further and to also consider vertically discontinuous shear wall systems, hence driving up diaphragm shear demands. Sometimes the project’s diaphragm unit shear is the controlling design parameter and drives the selection of I joist series, therefore it is important an engineer of record chooses an I-joist that is compliant for both gravity and diaphragm capacity demands.
Historically, I-joists flanges were deep enough to achieve minimum fastener penetrations listed in building code horizontal diaphragm tables, and equivalence to dimension lumber was generally accepted.
In recent years I-joist manufacturers have optimized their engineered flange material resulting in I-joist flanges that may no longer meet the minimum fastener penetrations.
With that said, some structural engineers have questioned the application of I-joists when used as framing members in engineered diaphragms. Interesting to note, fastener penetration is only one mode of failure related to diaphragm capacity and testing. A framing member’s primary resistance against diaphragm forces is the ability of an I-joist’s top flange to transfer shear forces between abutting panel joints and to resist cross grain tension stresses orthogonal to the flange.
Cross grain tension is induced when panel corners splay apart during induced rotation from shear forces. This cross grain tension mechanism is similar to the California Northridge Earthquake field observations of shear wall 2x mudsill splitting leading to the requirements of 3x sill plates for some shear walls.
To evaluate products not covered in the building code, the International Code Council Evaluation Service (ICC-ES) establishes minimum standards known as acceptance criteria (AC). A few years ago, ICC-ES updated their acceptance criterion for I-joist, AC-14, to require full-scale horizontal diaphragm testing to establish lateral load performance for products with flange depths less than 1-5/16 inch thick.
Weyerhaeuser has evaluated its current TJI joist product line with flanges less than 1-5/16 inch thick per AC-14 and provides diaphragm design information in ICC-ES report ESR-1153.
Section 4.15 and Table 2 (shown below) list the TJI joist series, equivalent nominal framing width, equivalent flange specific gravity, closest permitted nail spacing and maximum permitted seismic design capacities in pounds per lineal foot unit based on case orientation 1 through 6. Maximum diaphragm unit shear capacities are also listed for blocked and unblocked conditions.
For non-engineered structures, also known as prescriptive or conventional design, TJI joists are permitted to be used as diaphragm framing members per the governing building code provisions.
Refer to ESR-1153 for all applicable footnotes
Case 1 and 3 staggered joint panel layouts are typically the most common orientation for framing floors and roofs and for these two cases, the unblocked diaphragm unit shear capacities listed in Table 2 are identical to current building codes. For any wood framed project it is important an engineer of record provide assumed panel layout details, such as case 1 and case 3 layouts in their construction documents, so the framing is compliant with any design assumptions.
As diaphragm unit shear demands increase beyond unblocked diaphragm values, blocked diaphragm capacity limits are also given. For example, the maximum unit shear of the TJI 360, 560 and 560D series is 720 pounds per lineal foot for blocked diaphragm construction, which is the highest permitted for any TJI joist series.
Furthermore, only 1 row of panel edge fasteners is permitted in ESR-1153 and engineers are cautioned to not use high load diaphragm tables employing multiple rows of fasteners along panel edges with any manufacture’s I-joists. We have not evaluated high load diaphragm configurations, but believe the introduction of multiple rows of panel edge fasteners may propagate member splitting and a loss of structural performance.
One thing to keep in mind is that listed values are for seismic design and can be further increased by a 1.4 multiplier for wind controlled design. When project diaphragm needs exceed those listed in Table 2, the engineer of record should consider ‘zone framing’ with rectangular engineered lumber products such as Parallam® PSL, TimberStrand® LSL or Microllam® LVL or dimension lumber framing.
Please note, non-diaphragm fastener spacing guidelines for TJI joists are found in our technical bulletin TB-206 “Fastener Spacing in Trus Joist Engineered Lumber Products”.
In closing, it is also critical for an engineer of record to always review alternate product submittals for compliance for both gravity AND diaphragm member capacities, as evaluated in a current ICC-ES report.
And for those in the Canadian market, technical bulletin TB-155 “Horizontal Diaphragm Design with TJI Joists” has Limit State Design information.