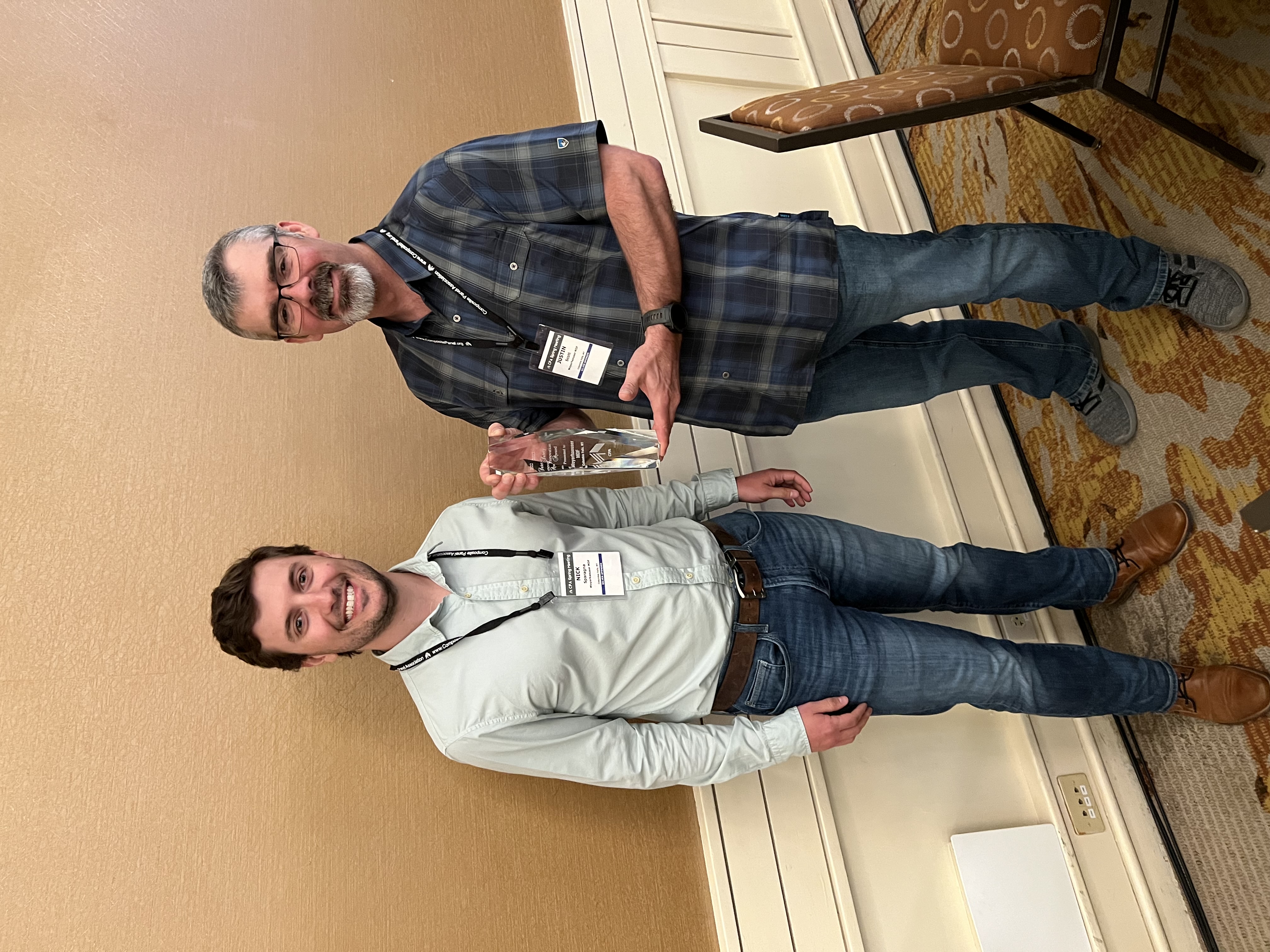
Nick Sparagna (left) and Justin Scott (right) represented Columbia Falls at the Composite Panel Association’s annual meeting in April and accepted CPA’s award for the 2022 Safety Innovation of the Year.
In 2019, Justin Scott joined our medium-density fiberboard mill in Columbia Falls, Montana, as a lead electrician. An important part of his job is conducting routine inspections of the site’s medium-voltage transformers — a hot, uncomfortable task due to the 40-cal suit and hood he wears to protect himself from electrical arc flash hazards.
Encouraged by the site’s emphasis on safety and innovation, Justin started looking for ways to improve the process and make it safer and more comfortable. His willingness to challenge the status quo soon led to a significant reduction in safety risk, along with gains in inspection efficiency and a top industry safety award.
Nick and Justin accept the award at the CPA conference.
HOT, HEAVY AND UNCOMFORTABLE
As temperatures soared his first summer on the job, Justin wondered if there might be a way to safely avoid wearing the bulky 40-cal suit by eliminating arc flash exposures altogether.
Arc flashes are well-known dangers in the electrical trade. These unintended electrical discharges occur when current travels along a path of ionized air between two conductive objects. They’re often caused by exposed wires, short circuits or otherwise damaged or faulty equipment. The resulting release of energy causes intense heat up to 45,000 degrees Fahrenheit, blinding light and a concussive shockwave. Arc flash injuries can be severe, including producing third-degree burns, permanent eye and ear damage, blunt-force trauma and even cardiac arrest.
“It wasn’t uncommon for me to wear the suit all day long,” Justin says. “We perform monthly and quarterly transformer inspections, which add up to about 430 transformer inspections a year.”
The mill’s 34 medium-voltage transformers step down 12,500 volts from the external grid to a usable 480 volts for the mill’s machine centers. Routine inspections are part of the team’s preventive maintenance procedures and allow them to identify issues that need to be addressed to avoid catastrophic failure and disruption of regular operations.
Inspection tasks include checking insulating-oil levels, looking for oil leakage and opening connection panels to check for hot spots with a handheld infrared sensor. Hot spots are often precursors of short circuits due to faulty wiring at connection points, failing components, unbalanced electrical loads and related issues.
“Each time we opened a panel, we were exposed to potential arc flashes,” Justin says. “Even if the suit had been comfortable, it was worth finding a way to eliminate that risk entirely.”
The innovation involved installing special infrared windows on the site’s mid-voltage transformers. The windows allow infrared sensors to take heat readings without opening the transformer’s protective paneling. Doing so significantly reduces exposure to potential arc flashes, hazardous electrical events, by more than 430 occurrences annually.
AVOIDING EXPOSURES
The team’s safety protocols — including the hot, heavy suit — followed industry standards for safe electrical work.
“I kept thinking I’d rather not be opening panels at all,” Justin says. “And electrical industry standards were evolving, increasingly encouraging a way to avoid panel opening by using infrared windows, a relatively new technology.”
Composed of calcium fluoride crystals, the windows allow thermal energy to pass through the opening while protecting against arc flashes.
“The idea is that we can point a handheld heat sensor through the window to get a reading on energized components,” Justin says. “If we could find a way to make it work here, we’d never need to open the panels during routine inspections.”
This Iriss infrared window is made of calcium fluoride crystals. It enables safer, more efficient and more comfortable identification of “hot spots” during routine inspections.
CAPTURING A WIN FROM A FAILED TEST
The Columbia Falls electrical team had previously experimented with the windows on electrical equipment closer to the machine centers but ran into challenges around optimal window placement for accurate temperature readings that led them to abandon the project.
Justin knew he could use the knowledge gained from those failed trials to inform the use of the windows on the site’s transformers. He looped in Nick Sparagna, electrical superintendent, and they posted the idea to our CuttingEdge innovation platform.
“The idea gained a lot of visibility and support, and the platform helped move the process forward,” Nick says.
To test the concept, Nick and Justin installed infrared windows on a single transformer panel, cutting out 4-inch holes and installing an infrared window in each.
“We wanted to be sure the handheld sensor could ‘see’ the critical connection points,” Nick says. “We figured out that some panels required two windows and others required only one. But we were getting accurate temperatures, so we decided to move forward and install the windows on the other transformers.”
Within months, the team installed 124 windows on its transformers, eliminating 432 potential arc flash exposures annually. What’s more, the inspections go more quickly now — and they’re more comfortable, too, not requiring any special PPE.
SAFER, MORE EFFICIENT AND AWARD WINNING
The innovation has been a big win both for the site and externally. In April, the Composite Panel Association named the project its 2022 Safety Innovation of the Year.
“This award truly represents the safety culture we’re building here at Columbia Falls and our commitment to eliminating hazards and reducing risk,” says Jordan LeFever, who was safety manager at the time (and is now safety liaison for Lumber). “It’s a great example of how safety success requires both idea work and teamwork.”
Justin and Nick traveled to CPA’s annual meeting in Tucson, Arizona, to accept the award on behalf of their team.
“I remember being there that first morning, wearing my name tag, and suddenly around 50 people approached and congratulated me,” Justin says. “It was crystal clear that safety mattered immensely to everyone there, but what struck me was their deep respect for Weyerhaeuser as a safety champion. I never truly grasped how much others admired the example we set.”