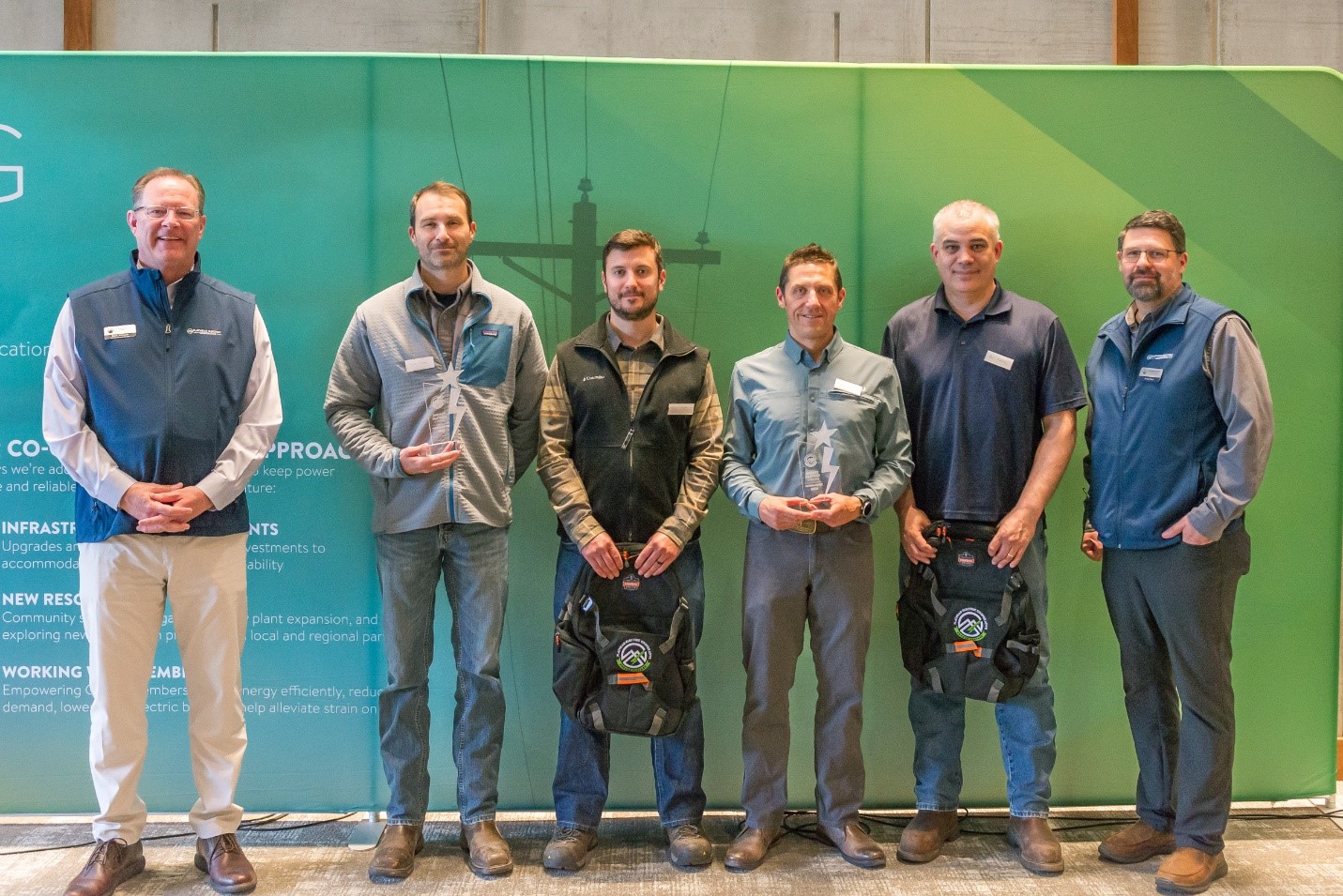
Pictured from left to right: FEC CEO Mark Johnson; Kyle Cram, Weyerhaeuser MDF plant manager; Nick Sparagna, Columbia Falls electrical superintendent; Jared Richardson, Evergreen-Kalispell complex manager; Ben Fabling, Kalispell electrical supervisor; and FEC Energy Services Supervisor Andy Masa.
When our three Montana manufacturing facilities teamed up to improve their energy efficiency in 2022, they set an ambitious goal: reduce energy usage by 2 percent annually. Thanks to teamwork, innovation and grit, they more than doubled their savings, reducing usage by 4.24 percent, or 1.38 million kilowatt hours, from October 2023 through October 2024. That’s enough electricity to power 187 homes for a full year.
Their hard work was rewarded. In April, Flathead Electric Cooperative named Weyerhaeuser its inaugural Energy Partner of the Year, recognizing the outstanding participation of our Kalispell and Columbia Falls teams in its Energy Smart Industrial Strategic Energy Management Program, offered in partnership with the Bonneville Power Administration.
“However impressive Weyerhaeuser’s economic impact is on the Flathead Valley, we are humbled by their commitment to managing energy use in ways that benefit all members,” Mark Johnson, CEO of Flathead Energy Cooperative, said in the press release.
The Columbia Falls team that worked to find ways to improve air compressor reliability.
COLLABORATING ON THE ROAD TO SUCCESS
For our Kalispell lumber and plywood mills and our Columbia Falls MDF plant, the secret to success was making energy leadership an integral part of their daily operations.
Nick Sparagna, electrical superintendent and energy leader at Columbia Falls, built an energy process focused on three things: a clear goal, an engaged cross-functional team and a repeatable structure to drive results.
“We meet regularly with electricians, millwrights and area leads from production to brainstorm, prioritize and measure ideas together,” Nick says. “The diversity of thought from this group has been crucial.”
In Kalispell, Ben Fabling, electrical supervisor and energy champion, emphasized the importance of culture and communication.
“We started by building an energy team with support from the mill manager and supervisors,” Ben says. “From there, we ran energy challenges, put up digital signage and offered prizes for ideas to build enthusiasm from the ground up.”
That enthusiasm quickly turned into action, thanks in part to Ben’s leadership and support from site management.
“Ben’s passion for energy savings projects has really brought awareness to the rest of the team about the impact energy consumption has on our business,” says Jared Richardson, Kalispell mill manager. “It’s created so much buy-in from the rest of the team.”
Weyerhaeuser Kalispell employees and external partners gather for a photo.
CROWDSOURCING BRIGHT IDEAS
Teams at Kalispell and Columbia Falls credit frontline employees with dreaming up the most impactful energy-saving projects. At Kalispell, one simple change had a big payoff.
“Supervisors got their teams on board with shutting down equipment when it wasn’t in use,” Ben says. “That alone saved between 3 and 5 percent in energy — just from increased awareness and participation.”
At Columbia Falls, Tom Larson, an electrician, upgraded more than 170 lights to LEDs between 2023 and 2024. Josh Smith’s reliability team introduced compressor training and maintenance plans that boosted performance and reduced waste. Meanwhile, Shiloh Keibler, plant superintendent, and Quinton Millward and Matt Salisbury, both functional area leads, led innovative work on refiner plate trials that significantly improved energy efficiency.
Each site used a range of communications tools, including SEM-provided training materials, our internal Innovation Tools and CuttingEdge to promote energy literacy and encourage ongoing contributions.
“We’ve made it easy for people to share wins,” Nick says. “From email updates to posted materials, we ensure good ideas are seen and celebrated.”
TRAILBLAZING FUTURE EFFICIENCIES
Neither team is content to rest on their laurels. They’re working on the next round of energy-saving projects, aiming to continue their progress.
The Kalispell team is upgrading a continuously running pump to operate on demand, using the same energy-saving control devices as a previous successful project. And teams at both sites continue to meet regularly to track progress and identify new opportunities.
“It’s not a one-and-done effort,” Nick says. “It’s about sustaining momentum and building a culture where energy performance is part of how we work every day.”
Many of the ideas generated through the process can be replicated at other sites, multiplying the impact of the teams’ efforts.
“You don’t need a formal program to start,” Ben says. “With leadership support, cross-functional teamwork and a little creativity, any site can make energy savings part of their operations and make a real difference.”