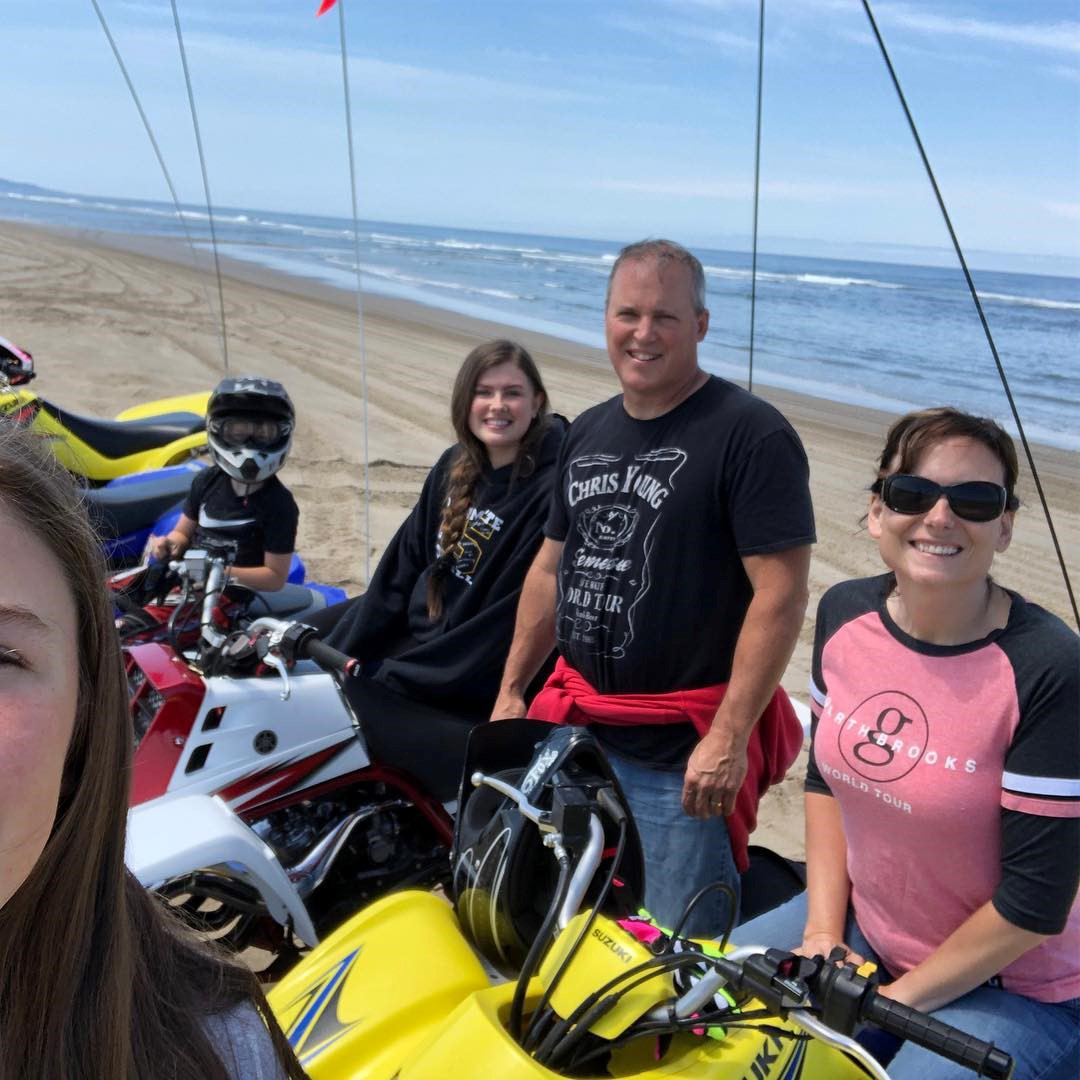
Zack with his family on the Oregon Coast. Zack started saw filing 38 years ago in his brother-in-law’s shop. Fresh out of high school, he joined the clean-up crew before fitting band saws and graduating to round saws. Zack joined Weyerhaeuser in 1987 and, after a stint with another company, returned to Cottage Grove in 1997 as a filer on the B shift. He became the sawmill’s head filer in 2015.
For Zack Allen, innovation isn’t a special project or something extra. It’s simply always on his mind.
“It starts with a problem or opportunity,” says Zack, filing team leader at our sawmill in Cottage Grove, Oregon. “And there’s always something that needs to be fixed for good or that could be done better.”
For Zack and his 11-person saw filing team, innovation often means squeezing out small gains in productivity through ever-greater precision. Fine-tuning a cut by just a few thousandths of an inch, after all, can significantly improve throughput and recovery — the amount of a log converted into a finished product.
But sometimes innovation requires refocusing from the micro to the macro. That was the case for Zack and team last year when big-picture thinking helped fix a long-standing safety and productivity challenge related to the gang-edger saw. It was one of many innovations that led to Zack being named one of five recipients of the 2022 Innovator of the Year Award. Launched in 2021, this annual award recognizes and celebrates employees who are driving improvements and fueling operational excellence through their ideas, actions and the innovative environment they help create on their teams.
“Zack is a very innovative leader who challenges his team to seek solutions to problems and continuously find the next level of performance,” says Brian Chaney, vice president of Engineered Wood Products and Innovation. “From step plate saws to gang speed control systems, his contributions have significantly impacted reliability at Cottage Grove.”
Zack hikes the Cascades with his wife Jill and youngest son, Jaxton.
SOLVING STUCK CANTS AND SHOOTERS
As the result of innovations over the years, Cottage Grove’s gang edger, a second-stage breakdown saw, cuts rough lumber at a rate of about 500 feet per minute. It’s an impressive improvement over its original design specification of 325 feet per minute, but the faster speed created a different problem.
Although the gang edger can process most cants — a log with its sides squared off — into rough lumber, not all logs come through with the exact same qualities. Density, grain patterns, knots and other natural variations can mean a particular cant needs a slower saw speed in order to avoid disrupting production.
Cut at the higher speed, some cants can become ‘shooters’ and hurl through the saw at destructive speeds. Others get stuck in the saws, halting production until team members remove the cant with chain saws, wedges and sledgehammers.
“We’ve always talked about a variable speed line that slows the cut for difficult cants,” Zack says. “But we had no way of knowing which cants could handle the higher speeds and which couldn’t.”
Despite the obstacle, the team kept looking for a solution. They added an amperage monitor so gang edger operators could see when the motors were drawing more energy to cut, which served as an alert for them to slow down the feed rate manually.
It helped, but the gang edger was still experiencing more than six hours of feed-related downtime a month.
“Stuck and shooting cants became one of those issues I was always working on in the back of my mind,” Zack says.
Zack and his family. While family time helps him recharge, he’s also energized by solving problems at work.
SENSING THE PROBLEM BEFORE IT’S A PROBLEM
Then Zack happened to receive a call from a vendor touting a system called SawADD, which uses sensors to gauge minuscule but significant blade deflections that indicate an inefficient cut’s early stages.
“We had installed a similar technology on our band saw and it worked well, so I called the vendor back,” Zack says. “I get many vendor calls, but most aren’t game-changers. This one seemed different.”
If nothing else, Zack figured the team might use SawADD to slow the production line if it sensed a problem cant, which would give the team time to adjust the feed speed manually. But if SawADD worked as promised, it would slow the line automatically, allowing it to run with fewer disruptions at greater average speeds.
Zack reviewed performance data with the vendor and connected with a saw filer at a non-Weyerhaeuser mill that had installed the system.
“Everything looked encouraging, so we assembled a team that included millwrights, electricians and operators to evaluate the system,” Zack says. “Then we ran our findings past mill and Wood Products leadership.”
A SawADD monitor screen shows saw speed and the radial and horizontal forces on the saws. The sensors detect difficult-to-cut cants and slow the feed speed, significantly reducing the number of stuck and shooting cants.
SAVING MILLIONS
After submitting a capital request and gaining approval, Zack and the Cottage Grove team installed SawADD on the gang edger last year.
“We knew it wouldn’t be a simple ‘plug-and-play’ installation,” Zack says. “Due to previous innovations, our gang edger is configured vertically rather than horizontally like most are, so we expected to face some challenges.”
Indeed, cants regularly knocked out SawADD’s sensors due to our gang saw’s novel configuration. After three months of trial and error in consultation with the vendor, the team found a new type of sensor that could be positioned farther away without affecting performance.
The results were immediate and impressive, generating more than $2.6 million in annualized OpX savings by:
- Reducing stuck cants by 90 percent and shooters by nearly 40 percent.
- Decreasing downtime from feed-related issues by almost 50 percent.
- Increasing average feed time by 18 feet per minute.
- Reducing safety risks associated with downtime-related upset conditions.
“While SawADD might be more impactful than many innovations, it started the same way they all do: by asking ourselves daily what we can do differently and being open to new ideas,” Zack says. “And it’s not just me. Looking for new ways of doing things and trying out new ideas is how we roll at Cottage Grove.”